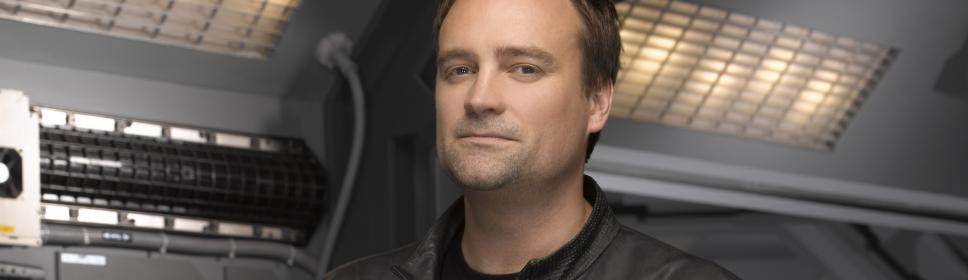
First Impressions Cold Casting
Today I started to experiment with the casting method known as cold metal casting, or cold casting for short. Unlike traditional metal casting which uses molten metal, cold casting involves the bonding of metal particulates with liquid resin. The end result is a combination of resin and metal to create the effect of metal. The metal powder can be either mixed directly into the resin, or applied only to the surface by dusting the mold prior to applying resin.
So far I have only tested dusting molds with metal and backing with straight resin. It is this dusting of the mold which gives the most important layer in the final finish, and so this is where I wanted to focus. This week I will follow up with additional tests to apply a thin backing layer of metal filled resin (1:2 ratio), and then straight resin for the core of the casting. Mixing metal powder into resin weakens the bond of the final cast, and so the solid resin core is going to give the final casting it's strength.
Ultimately I am looking to have three layers to my cold casts:
- Surface layer of 100% metal powder,
- Thin wall of metal filled resin
- Solid resin core
I also need to pick up some steel wool for bringing through the luster of the metal castings.
Print | Share | Comment